Recently, I had the great opportunity to visit the Blancpain manufacture in Vallée de Joux, to discover how their watches are produced and who is behind this craftsmanship. Read about my experience and see many unique photos below.
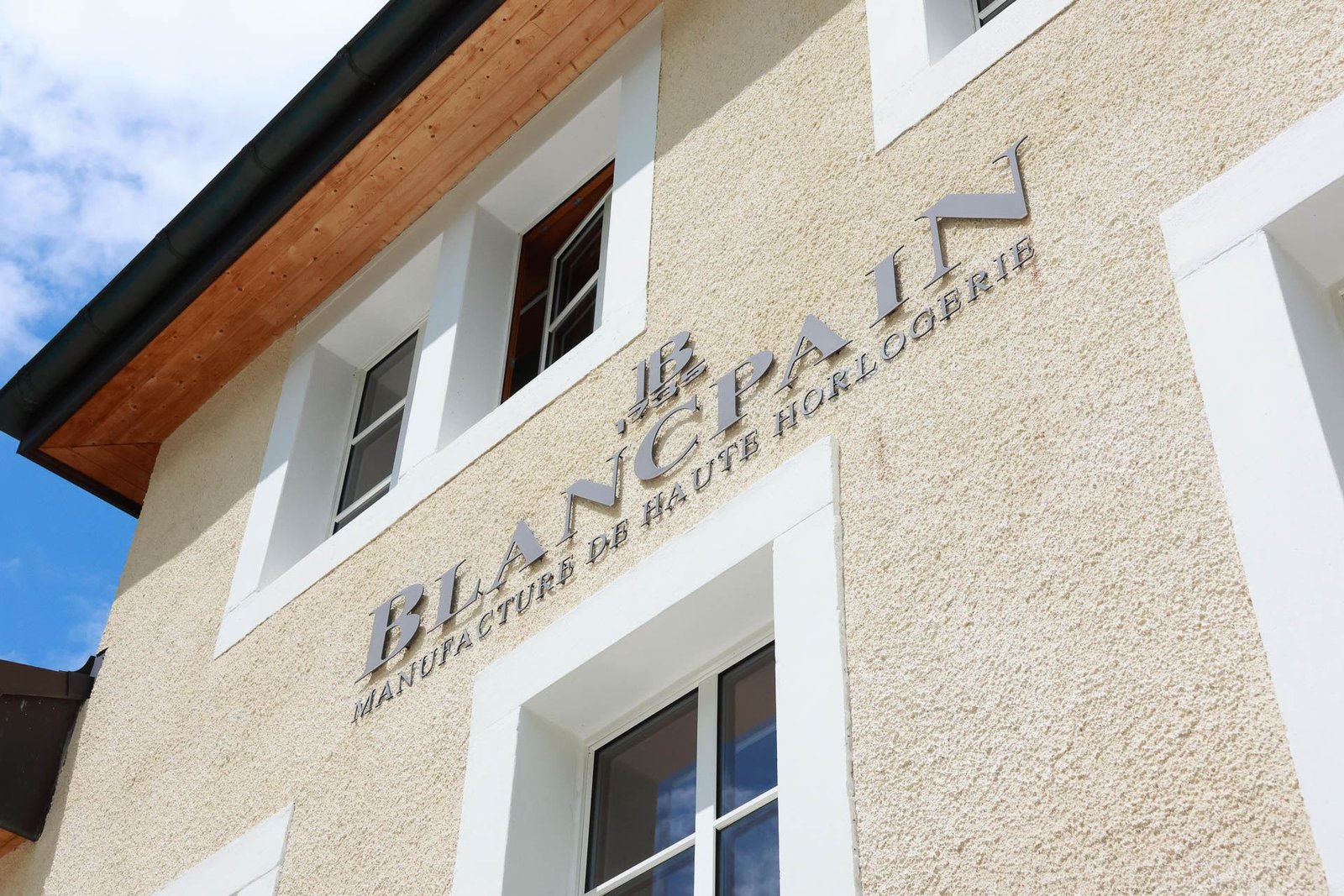
The watch world is multifaceted and contrasting. From a consumer’s perspective and what we see on social media, it appears to be a glamorous world for many. But the other side is often very different. Therefore it’s interesting to discover where and how these miniature objects are produced and who is behind this craftsmanship. To figure this out, at the invitation of Blancpain, I went to Switzerland to find out all the details. We flew to Geneva, spent the night in Lausanne, and the next morning drove to the Blancpain manufactory in Vallée de Joux. The journey to the manufactory takes about an hour, and already on the way, you realize how different the glamorous world of watches is from where they are produced. Most of the route runs through the picturesque Swiss hills, where it is much easier to meet a cow than a person. Peace, tranquility, and beauty. After less than an hour’s drive, the name Le Brassus appears on a sign. A small Swiss village, not particularly noticeable at first glance, but it is the birthplace of Swiss watchmaking and is still home to the most famous Swiss watch manufactories. We enter Le Brassus, and the first thing visible from the road is the Patek Philippe manufactory. After half a kilometer, we pass Audemars Piguet and head further towards Le Sentier, the neighboring village where most of Blancpain’s watch production is located. There are three facilities: in Le Sentier, where movements are designed, tested, and all the main watches of the brand are produced, such as the Fifty Fathoms or the classic Villeret; the atelier in Le Brassus, which is responsible for the production of the most exclusive and complex Blancpain watches; and one located in Delémont in the Swiss Jura, which is the Blancpain watch finishing division.

The main production at Le Sentier is more secretive, with few visitors allowed inside, and filming is prohibited. In this building, the full production cycle of the watches happens, from the conception and design of the movements by watchmaking engineers and analyzing the performance of watch components in the purpose-built laboratories, to movement assembly, final encasing, and quality control. The components for the movements are also produced in-house, as well as special tools for the watchmakers who assemble the movements. The after-sales service team of watchmakers is also located here. In total, more than 700 people work in Blancpain’s Le Sentier workshops.
We entered the building and headed straight to the cellar. Turning right, we walked along a long corridor, with our first stop being a large room filled with raw materials used for cutting movement parts, mainplates, rotors, and cases. Adjacent to this room is where special tools for internal use are produced. We then moved to the room where milling machines cut the mainplates for all Blancpain calibers. Although the cutting process itself is relatively fast, it takes about eight hours to set up the machine for a specific mainplate. In another room, we observed the creation of rotors. Each rotor starts as a 15-gram piece of gold and emerges as a 5-gram rotor. The remaining gold is collected in a dedicated trash can for recycling and reused in production. Blancpain produces rotors exclusively from gold or platinum and also manufactures rotors for other brands, including those outside the Swatch Group.

Our tour continued on the upper floor, where watches are assembled, tested, and prepared for boutiques. Before entering the large open space with huge windows, we donned white coats and shoe covers. Sterile cleanliness is paramount in watch assembly areas. Passing by one watchmaker’s table, I saw her assembling a new titanium Fifty Fathoms 42 mm with a black dial.
At the end of the tour, we boarded a minibus and traveled to Le Brassus, the second Blancpain manufactory, more accurately described as an ‘haute horlogerie atelier.’ The building resembled a luxurious estate rather than a watch production facility. This historic Blancpain building, known as “The Farm,” was originally an old mill bought by Louis-Elysée Piguet in 1891. The interior, rich in wood, feels like a luxury home and matches the style of Blancpain’s boutiques.

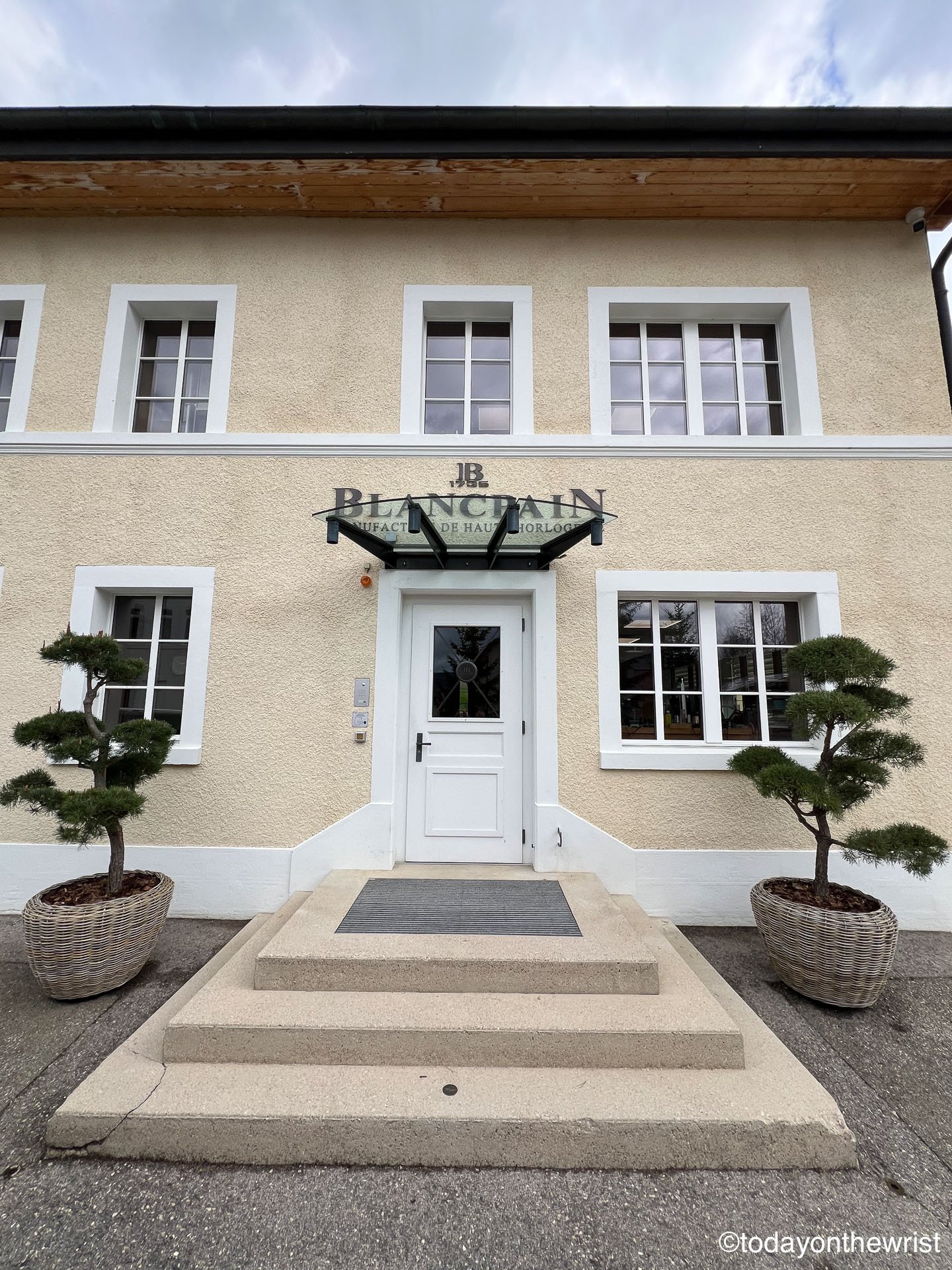
Within these walls, master watchmakers dedicate themselves to grand complications, such as minute repeaters, split-seconds chronographs, carrousels, tourbillons, and ultra-complex calendars like the Equation du Temps Marchante and the Calendrier Chinois Traditionnel. The Farm also houses Blancpain’s Le Brassus decorating and engraving workshops, as well as those for decorating components of prestigious movements.
Tourbillons & Carrousel workshop
Each complication has its own workshop. We started in the area where tourbillons and carrousels are created.


If you own a tourbillon watch from Blancpain, then it was most likely created on the table shown in the picture below.

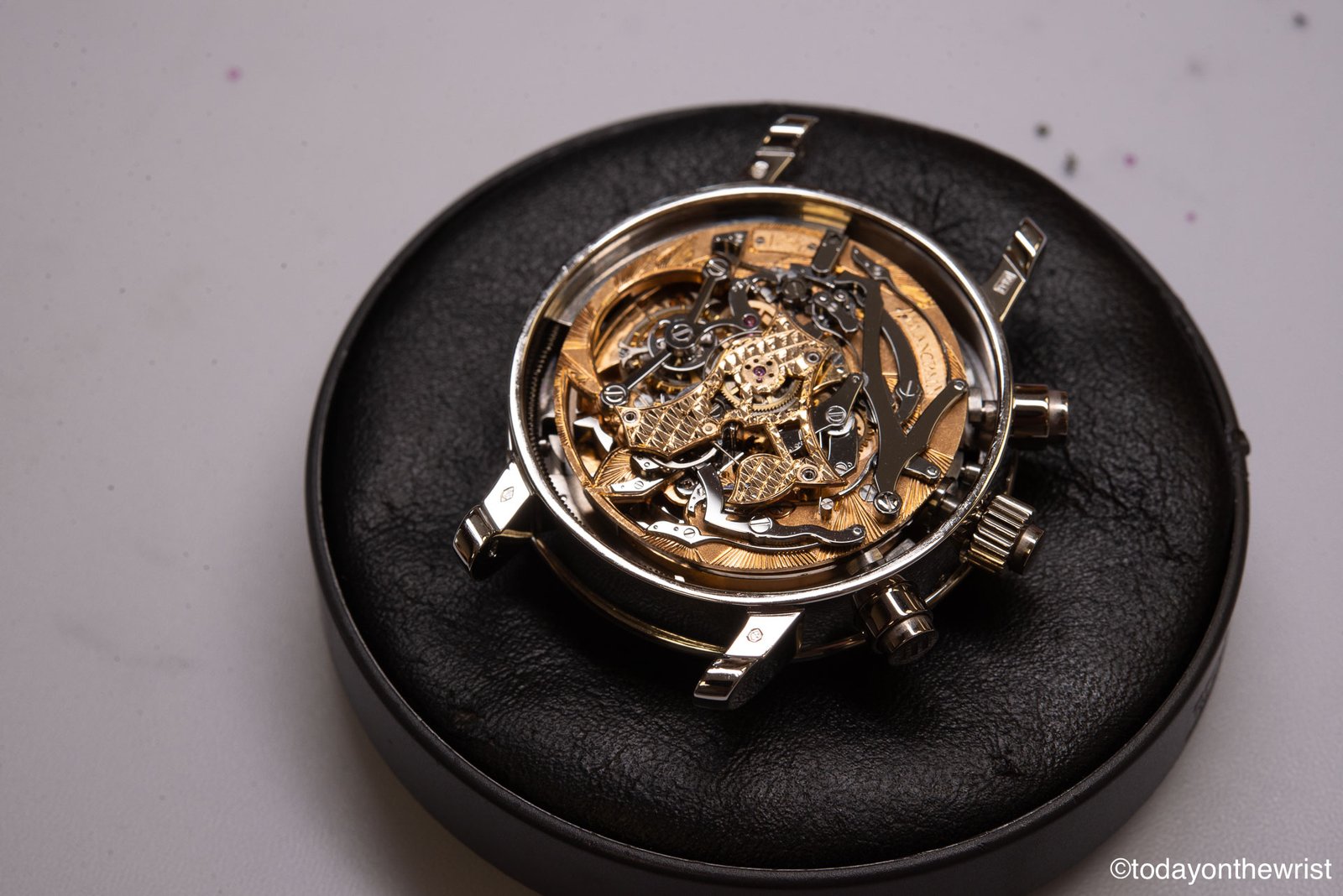
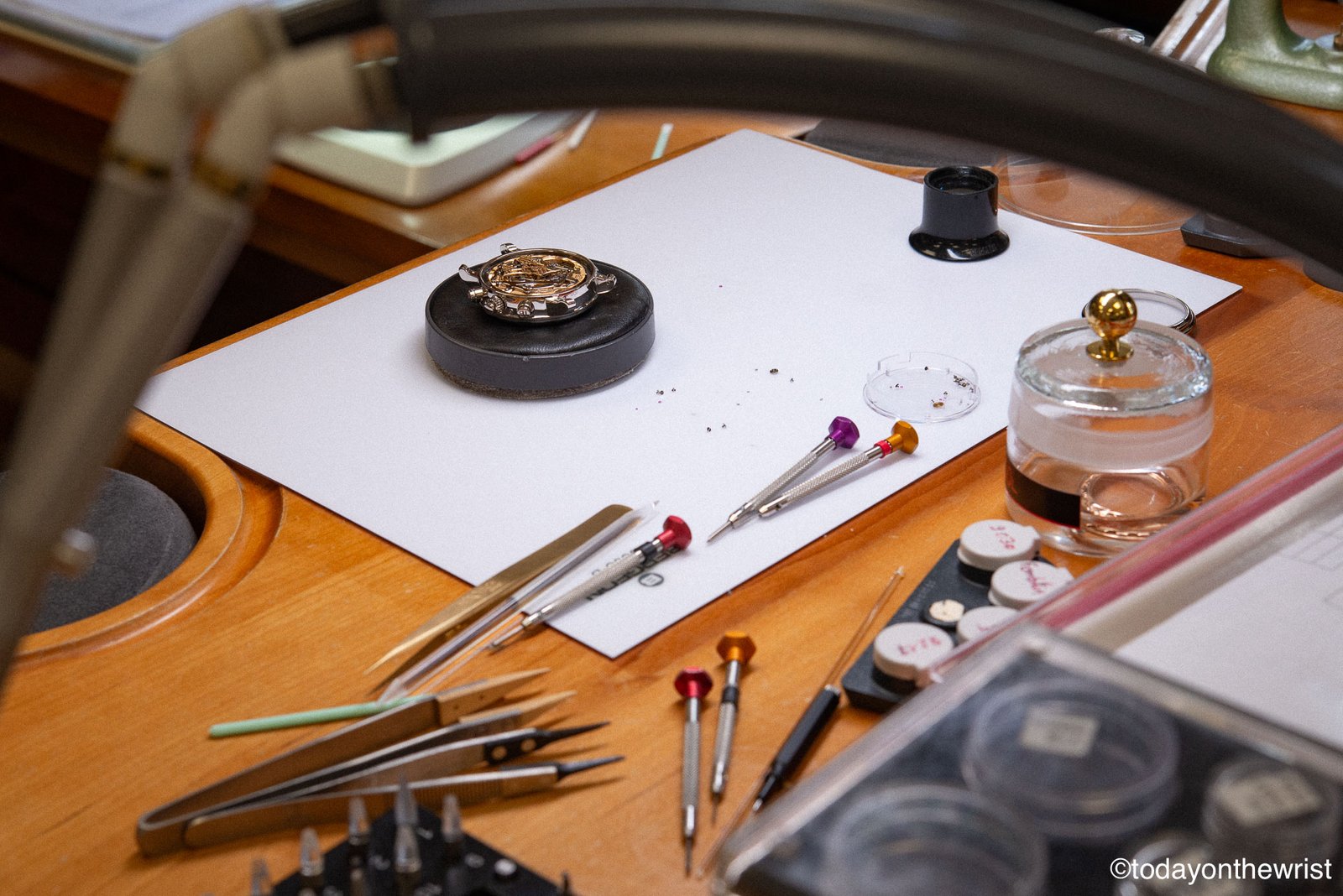
A watchmaker is working on the Traditional Chinese Calendar watch.


Répetition Minutes & Complications workshop
Next stop is the workshop where minute-repeaters are created, one of the most difficult complications to make.
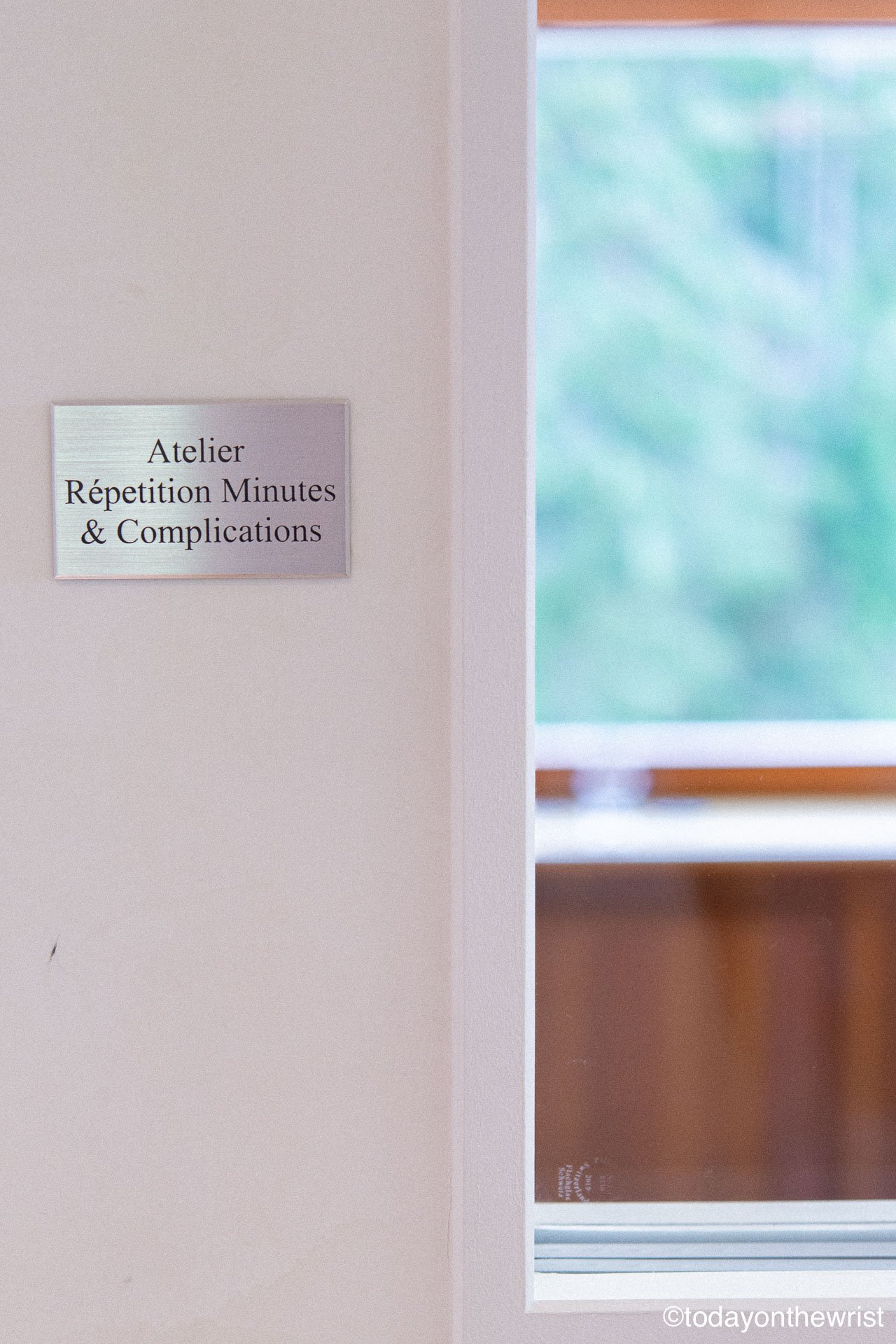

It takes one watchmaker an entire month to create a minute repeater.
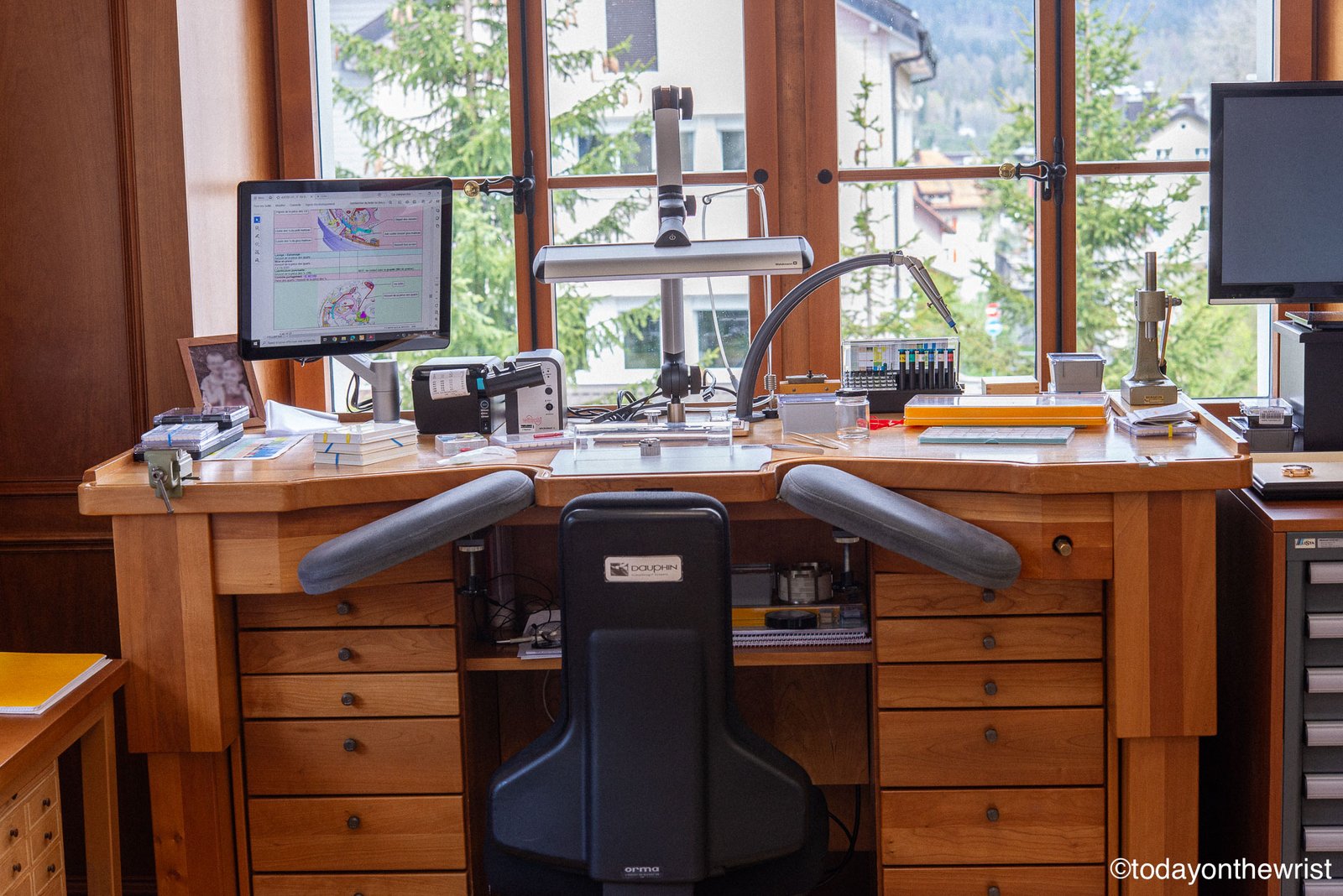


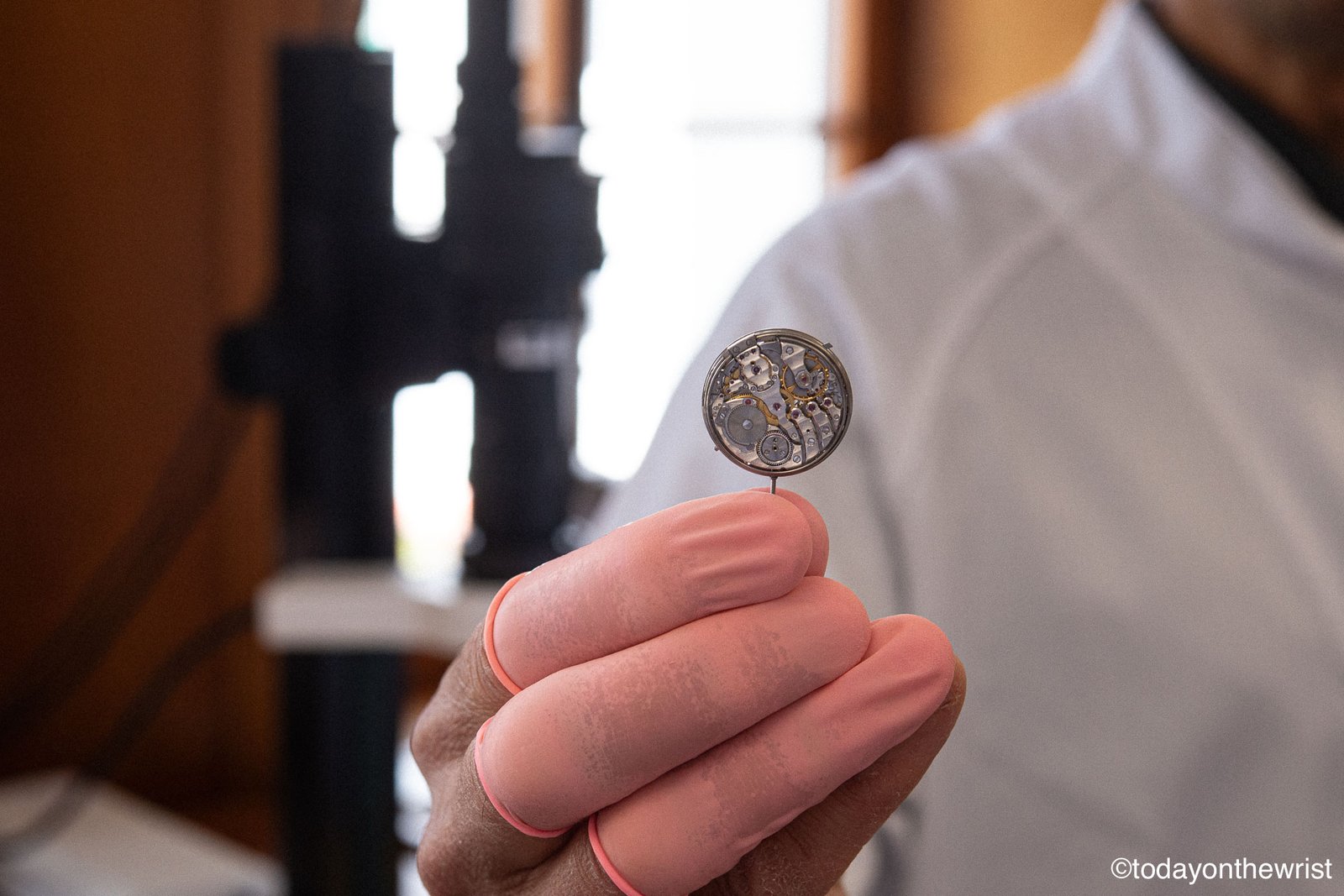
In the upper picture is one very fine and among the thinnest minute repeater movements out there.
Decorating and engraving workshop
This is where Blancpain artists devote themselves to various forms of expression in watchmaking, particularly engraving motifs on dials and movement components, and painting miniatures in enamel. Alongside traditional techniques, they delight in introducing processes previously unknown in haute horlogerie, such as the Japanese art forms of shakudō and binchōtan, and damascening. All the watches in the decorating and engraving workshop are unique, often designed to order. When we entered the room, the artists were working on some unique pieces, so we were only allowed to photograph a few items to maintain the privacy of those special orders.

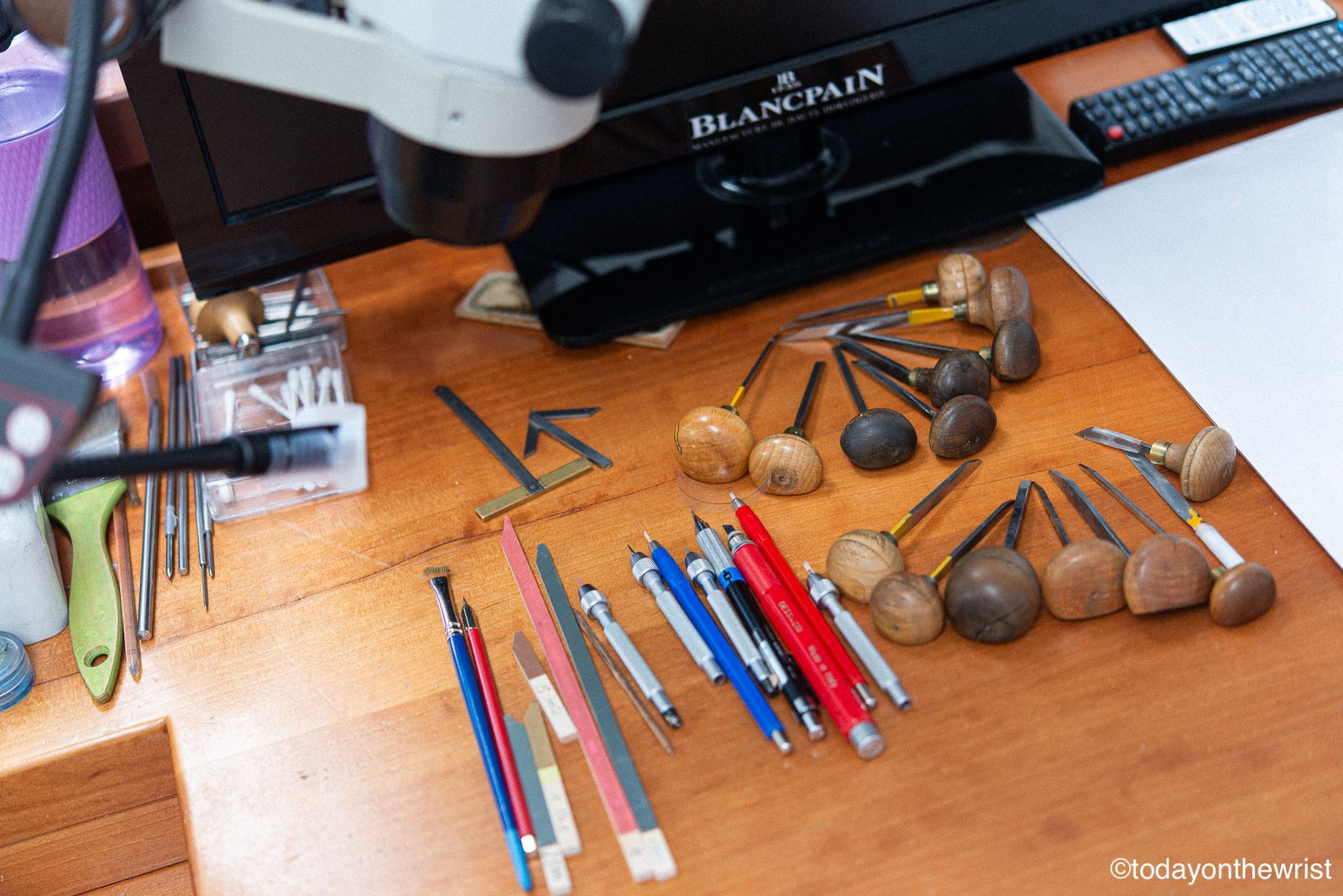
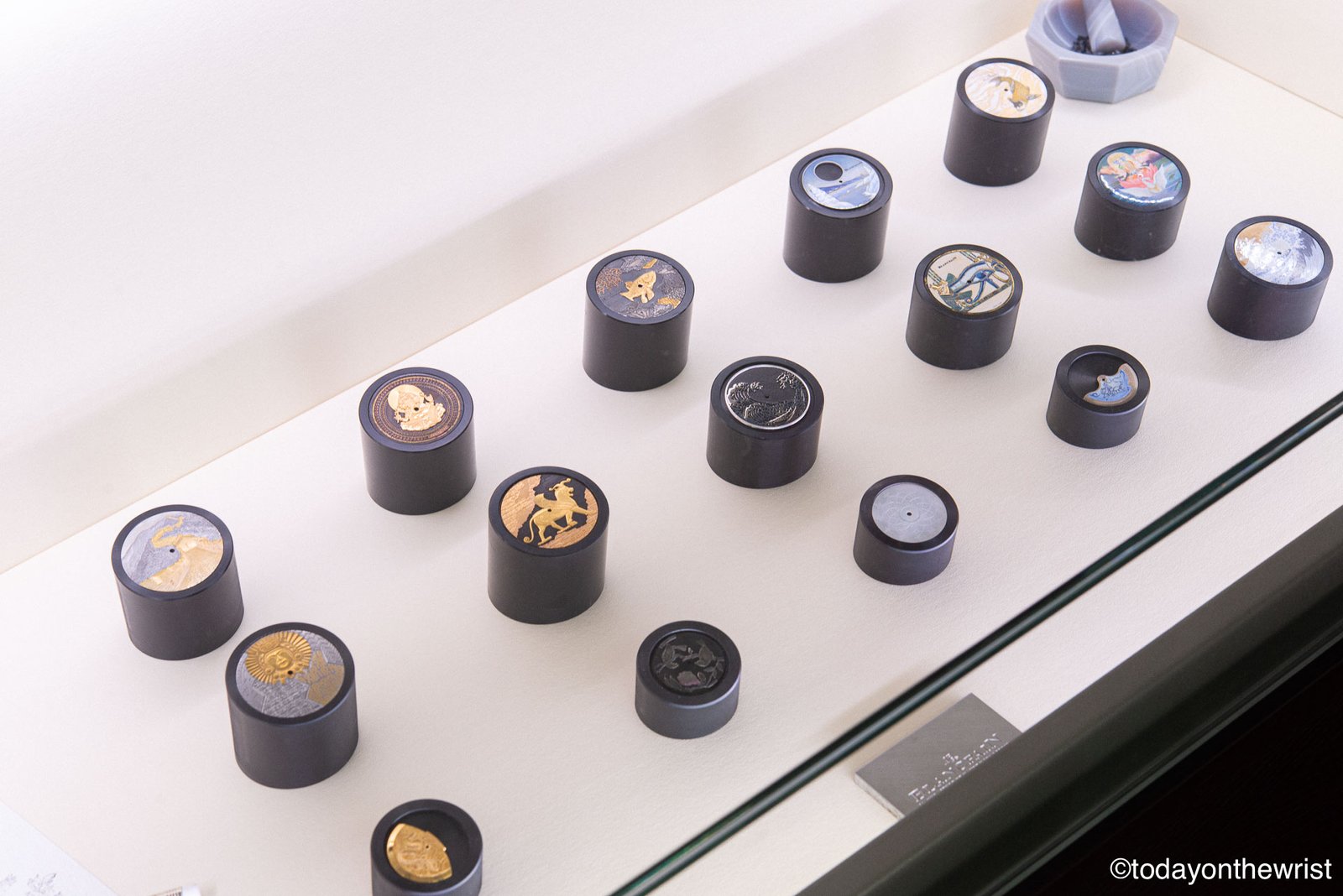
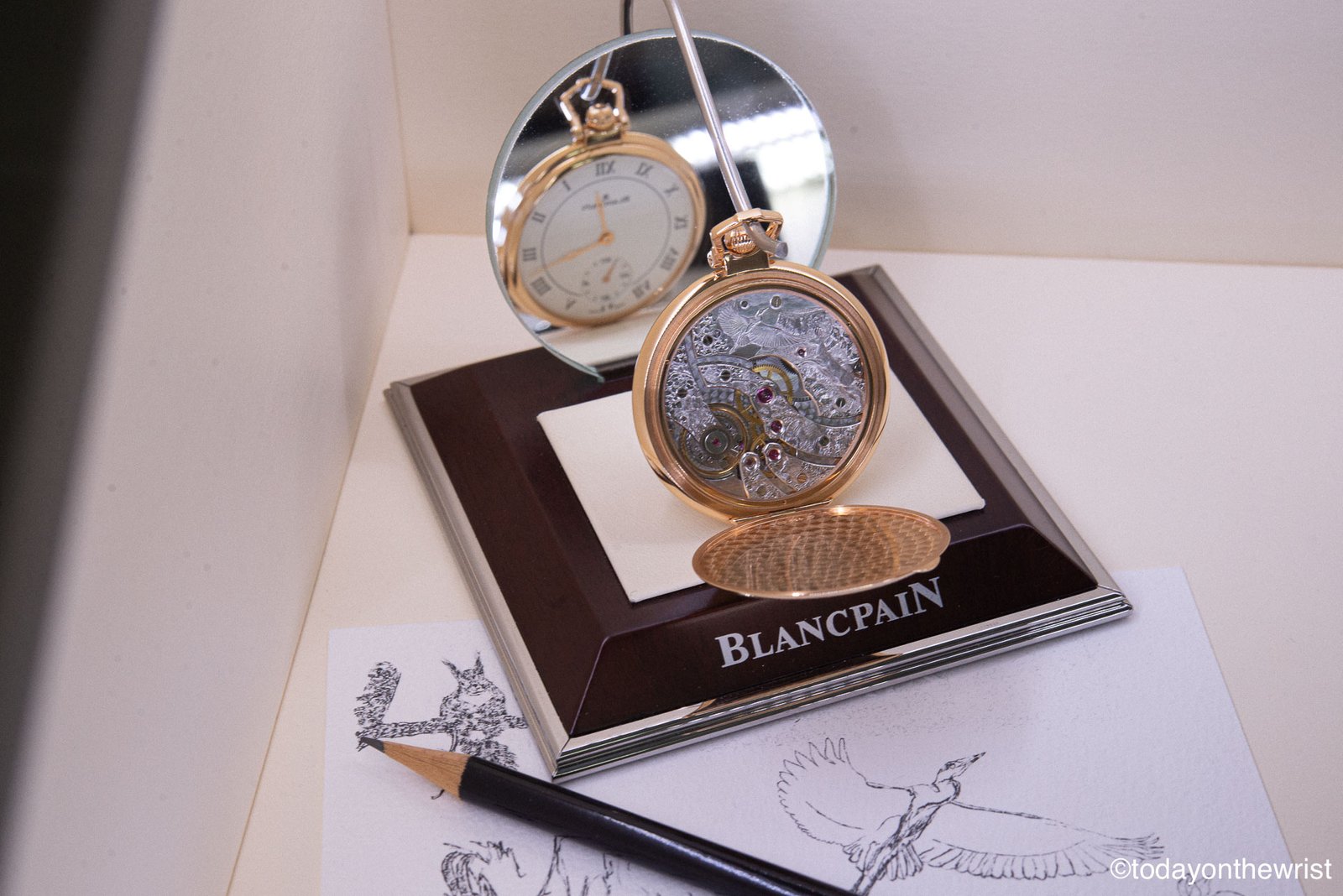

We also saw how different parts of the movements, like movement bridges, oscillating weights, and mainplates, are decorated. In the pictures below, you can see the many traditional decorating tools that are still in use here.
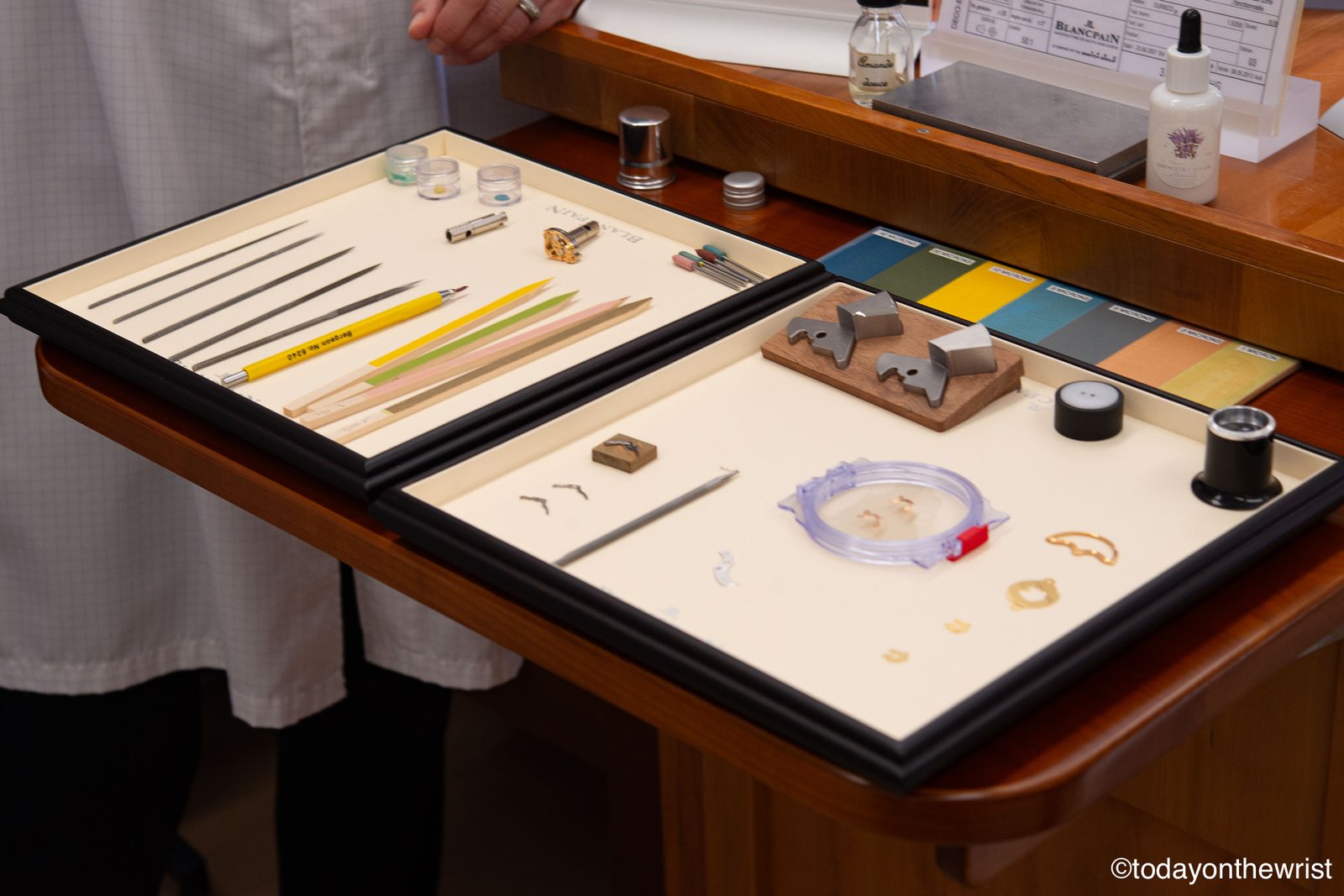
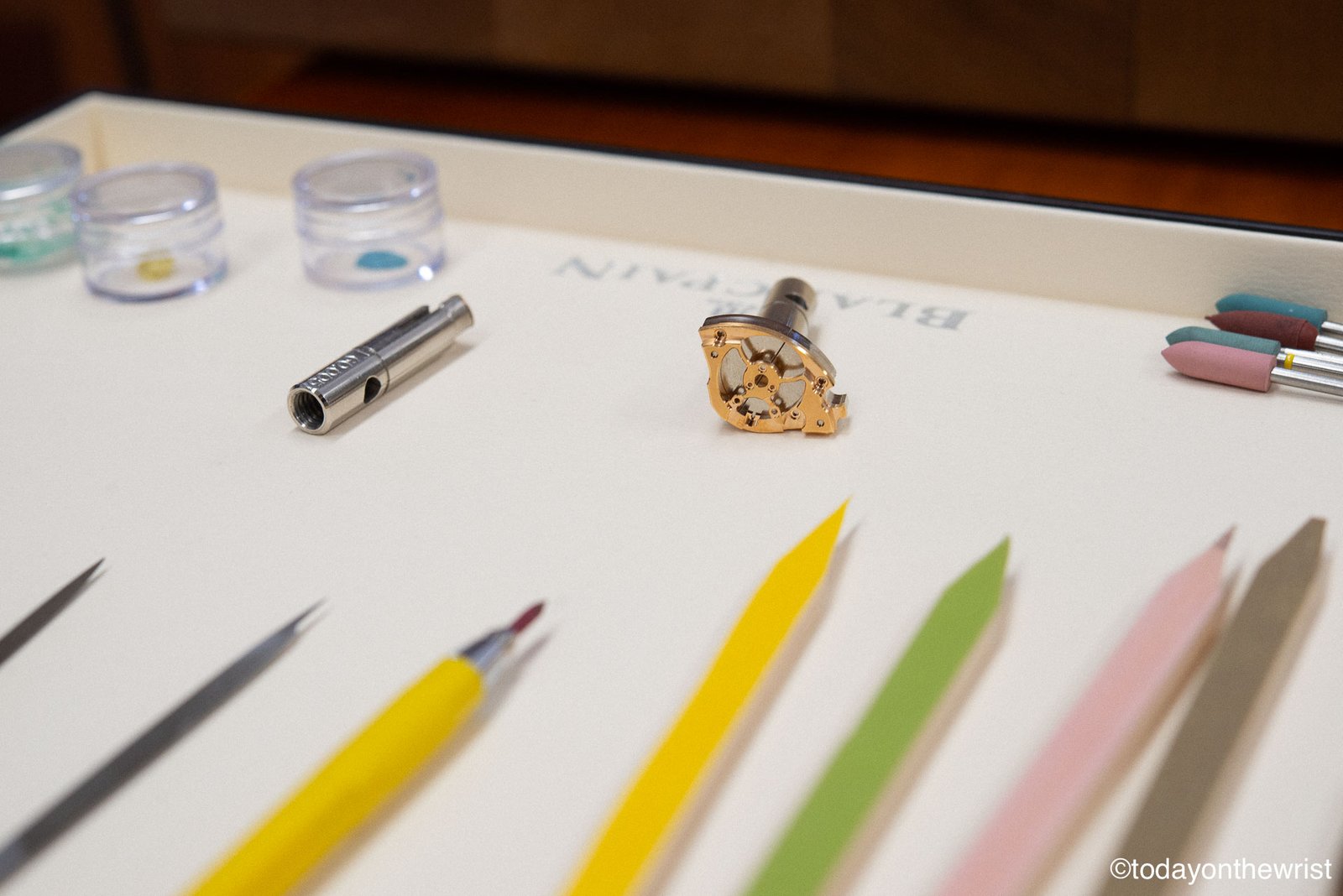
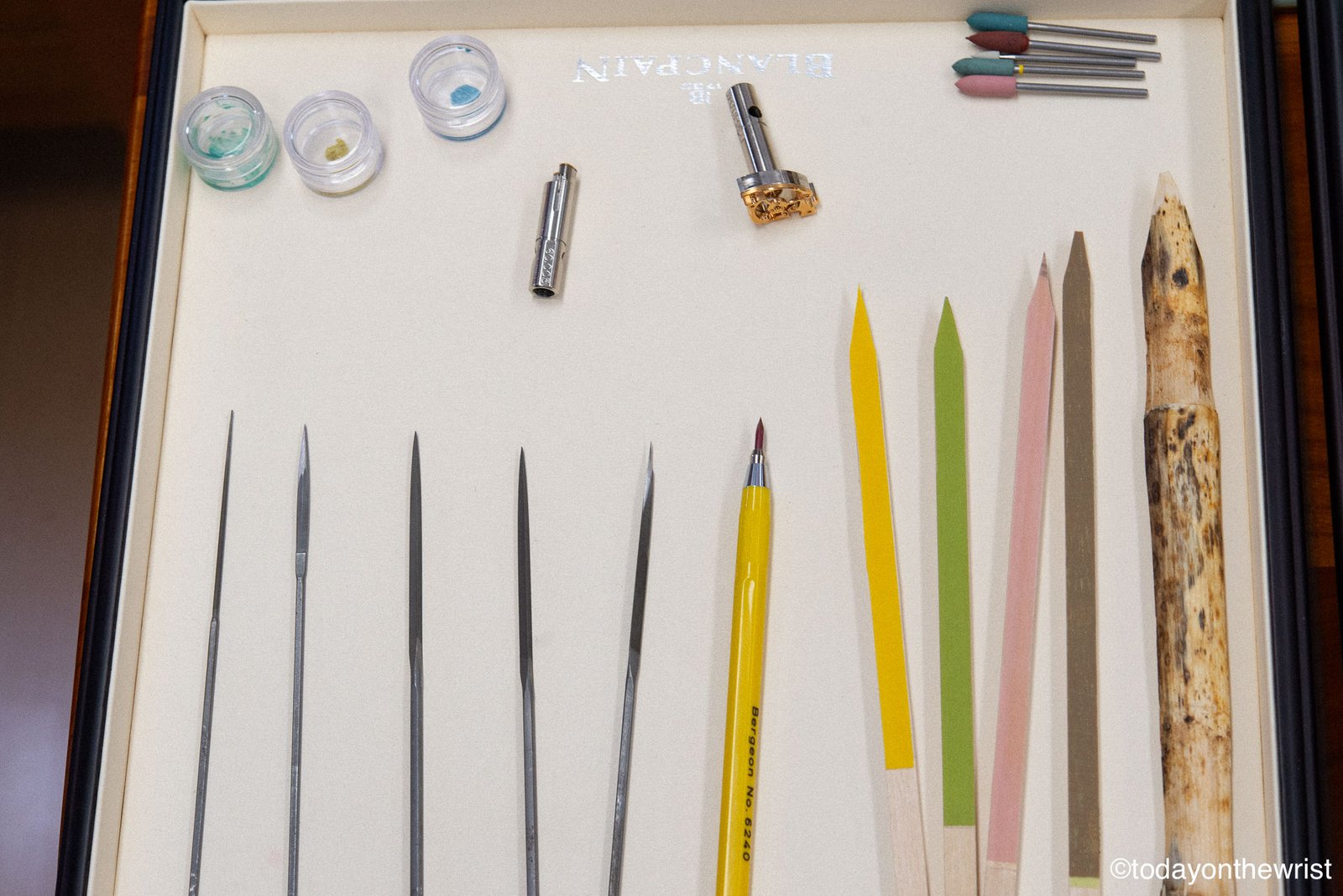
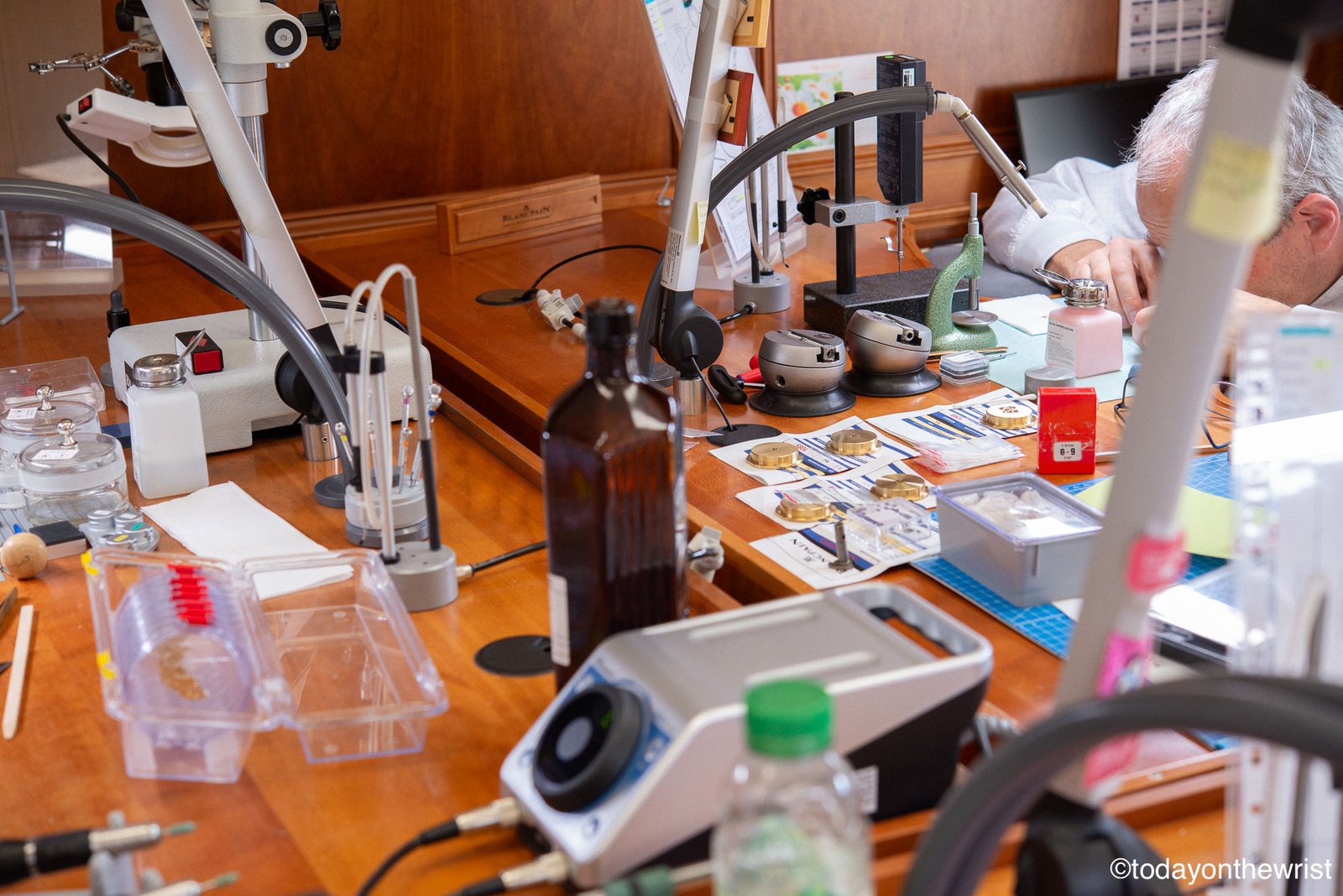
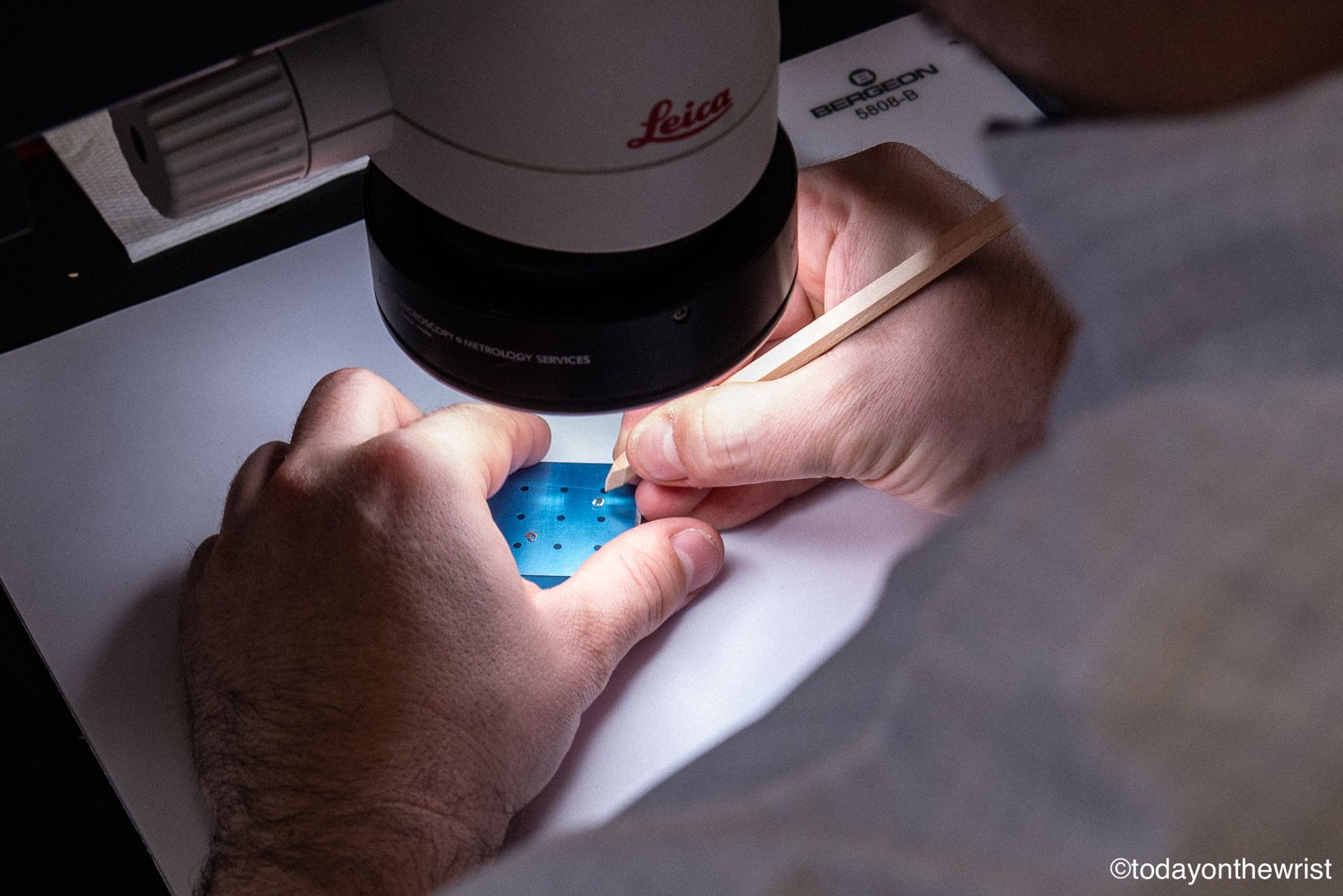

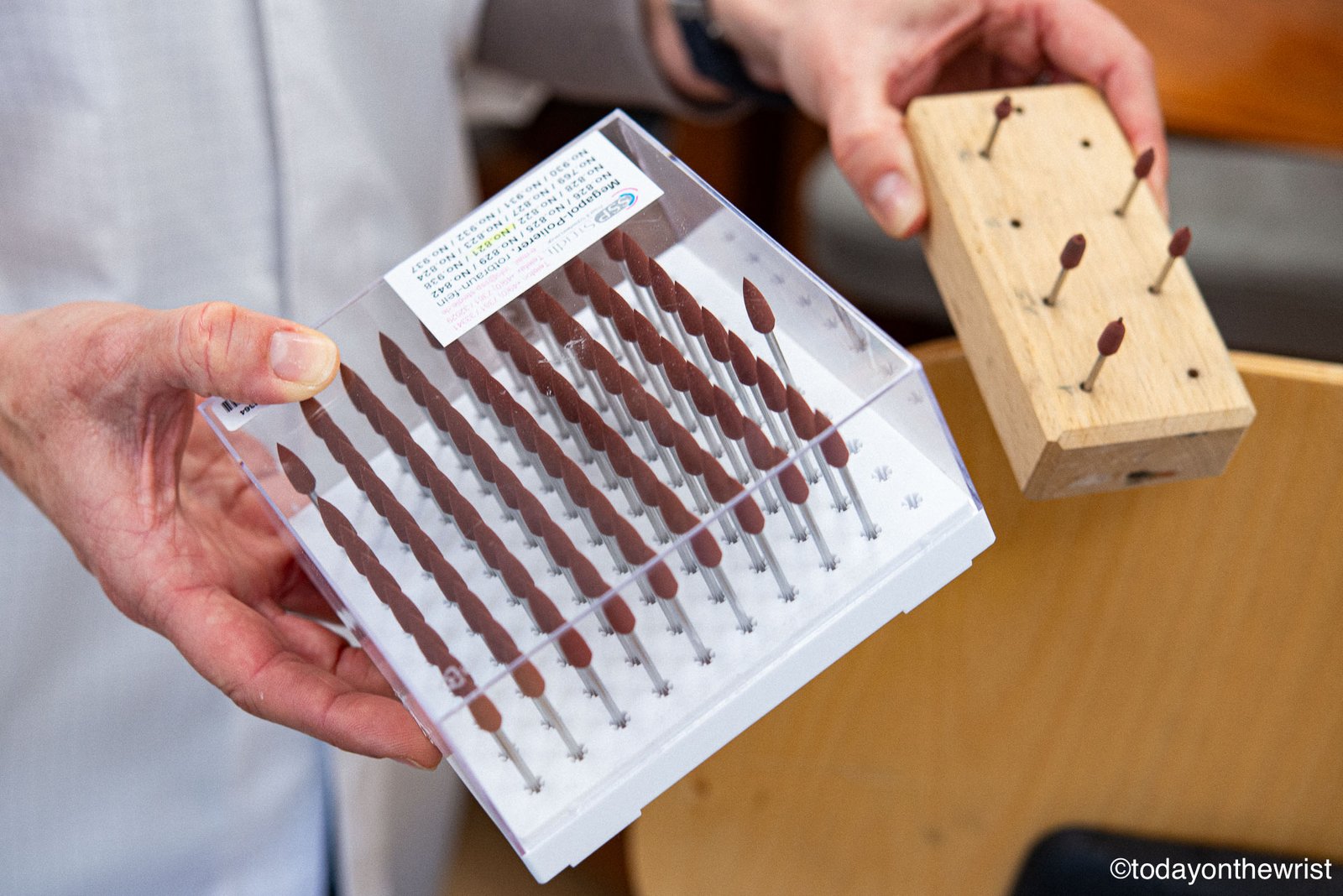

Vintage/restoration workshop
In the same building, there is also a vintage and restoration workshop. This department, dedicated to the service of heritage pieces, offers an array of services to ensure the longevity and authenticity of these treasured timepieces. The authentication process takes approximately 10 days. For those requiring more extensive work, the conservation and revision of watches can take up to 3 months, while full restorations can take up to 6 months. When we entered the room, there were a few historical pieces on display, such as the Blancpain U.S. NAVY, the Aqua Lung, Fifty Fathoms No Radiation, and the Fifty Fathoms Bundeswehr Kampfschwimmer. As a big fan of these historical Blancpain watches, it was great to see them together in one place.


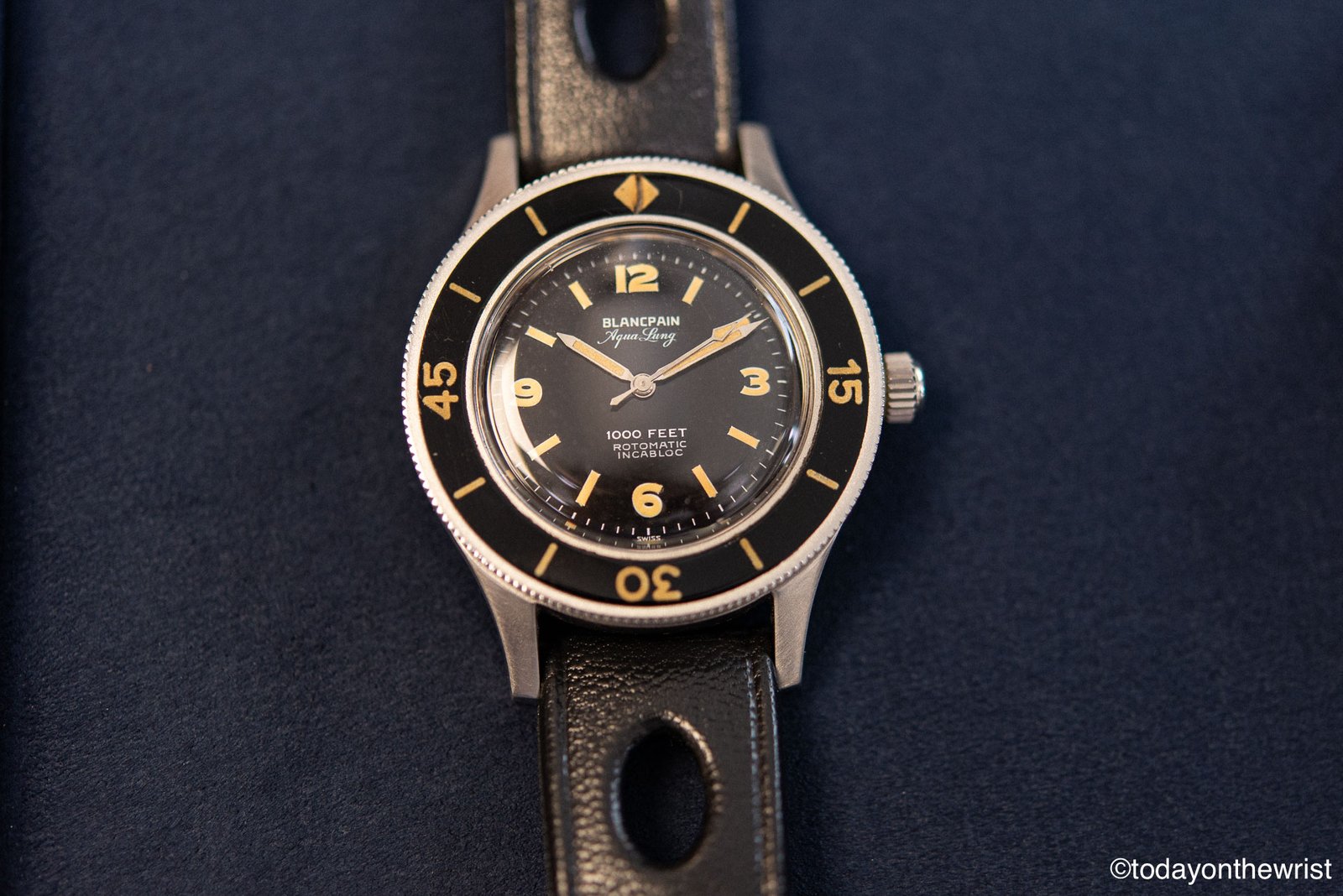


Moving from workshop to workshop, you notice various interesting details in the corridors, observe the concentrated work of the watchmakers, and absorb the calm and deliberate atmosphere of the building. I’ve tried to capture all of this in the shots below.



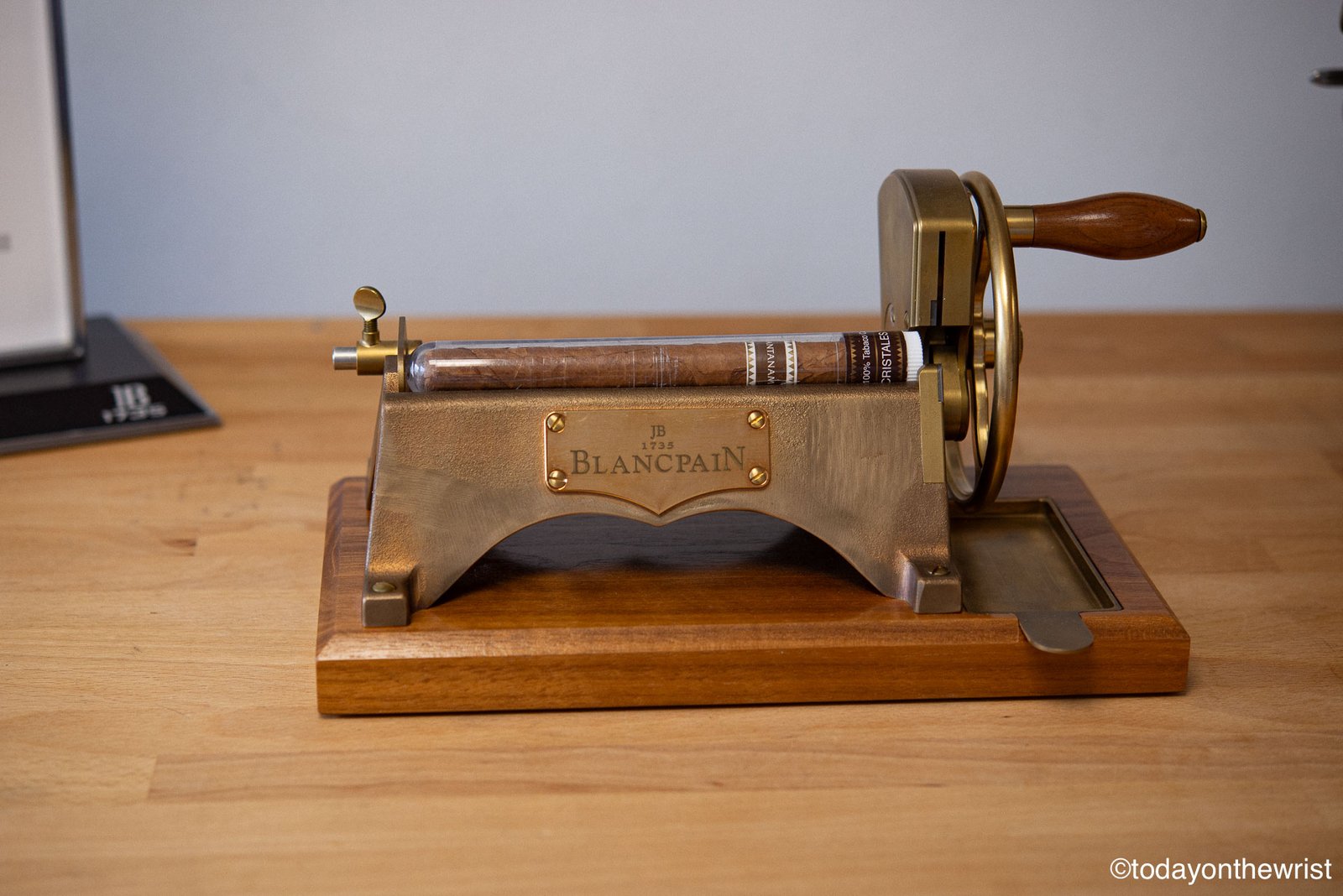

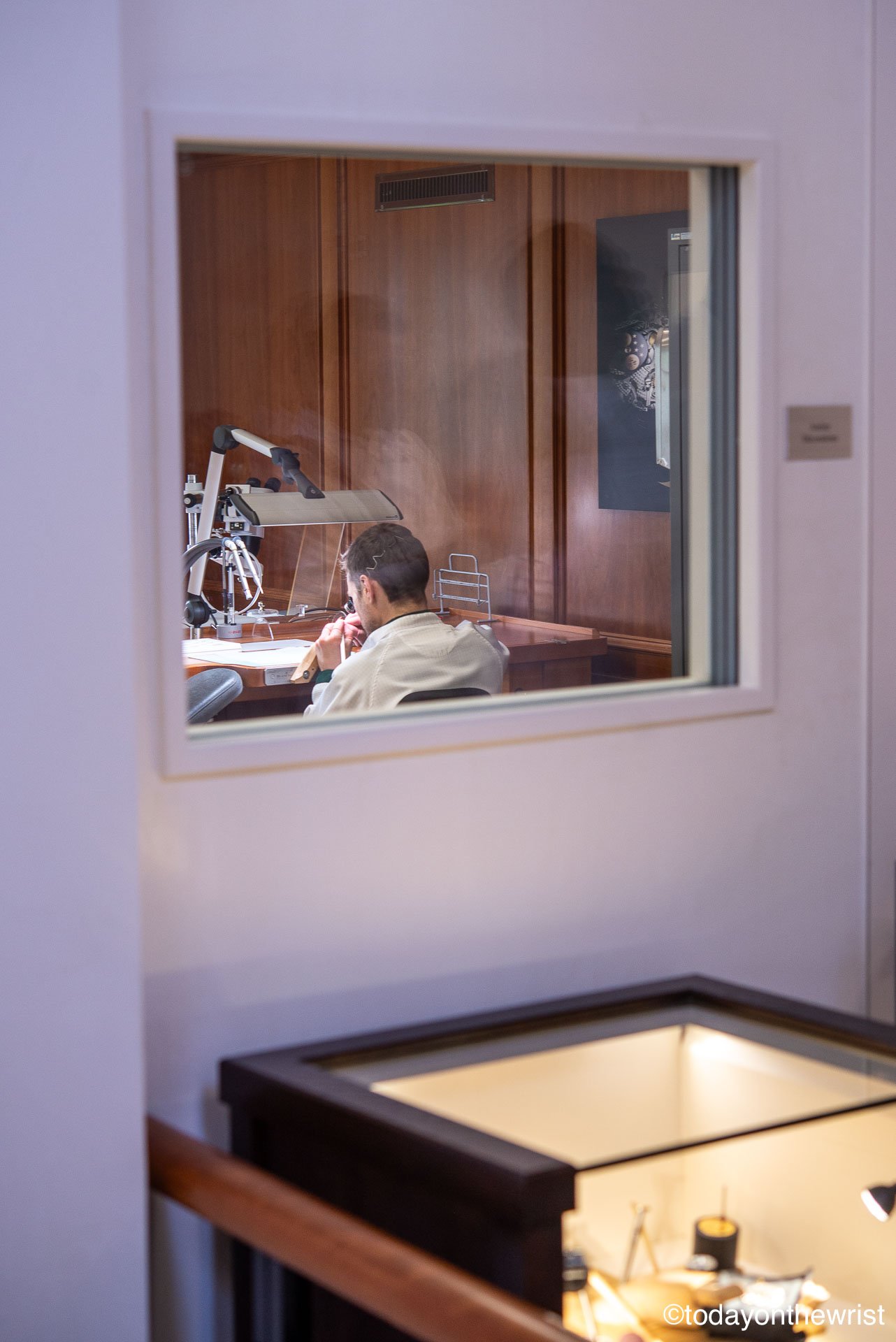
After finishing our tour of the facility, we enjoyed a glass or two of champagne on the terrace, followed by an amazing lunch. Of course, we also had the opportunity to explore modern watches from the current collection.




Here is my selection of three completely different watches from that day.
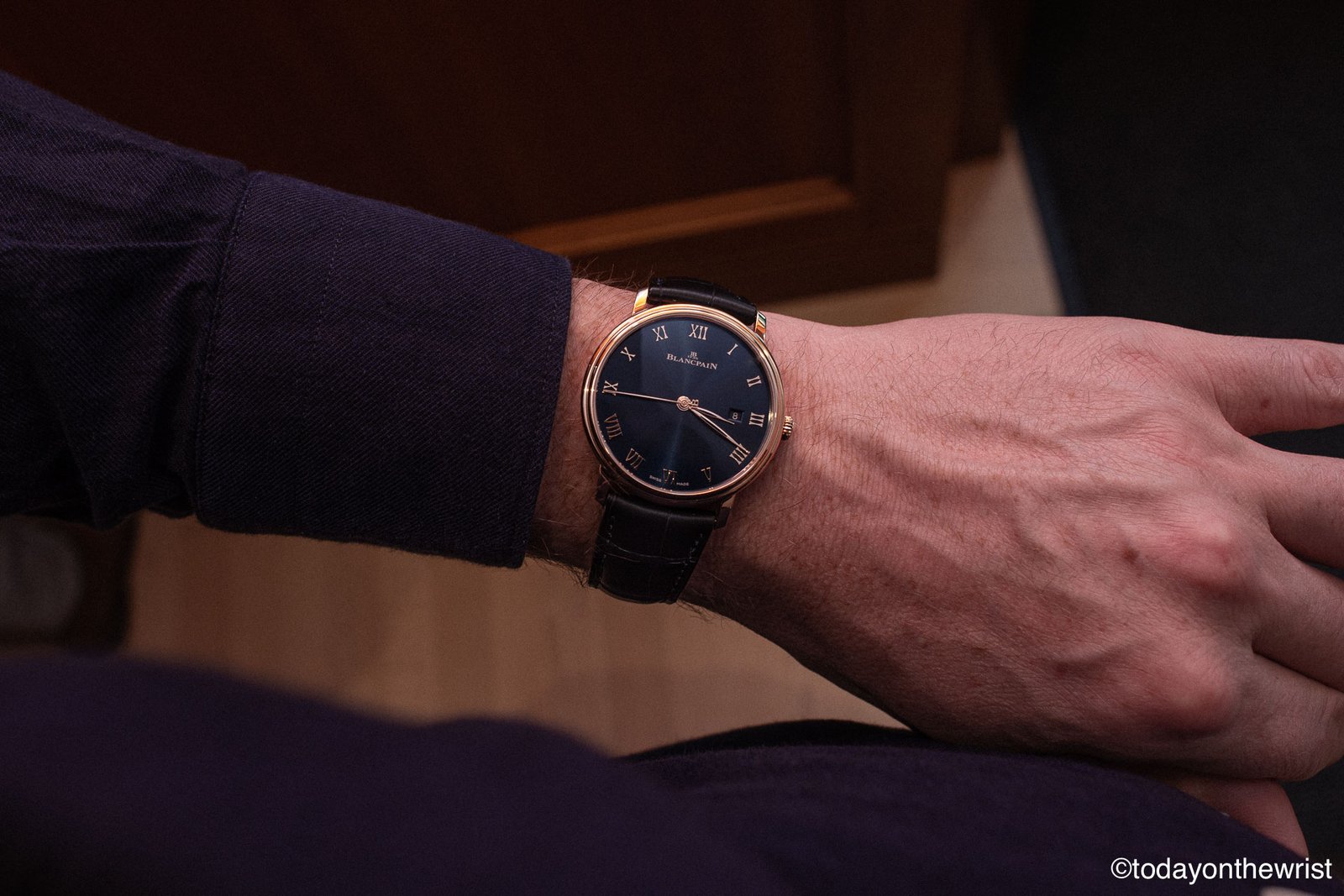

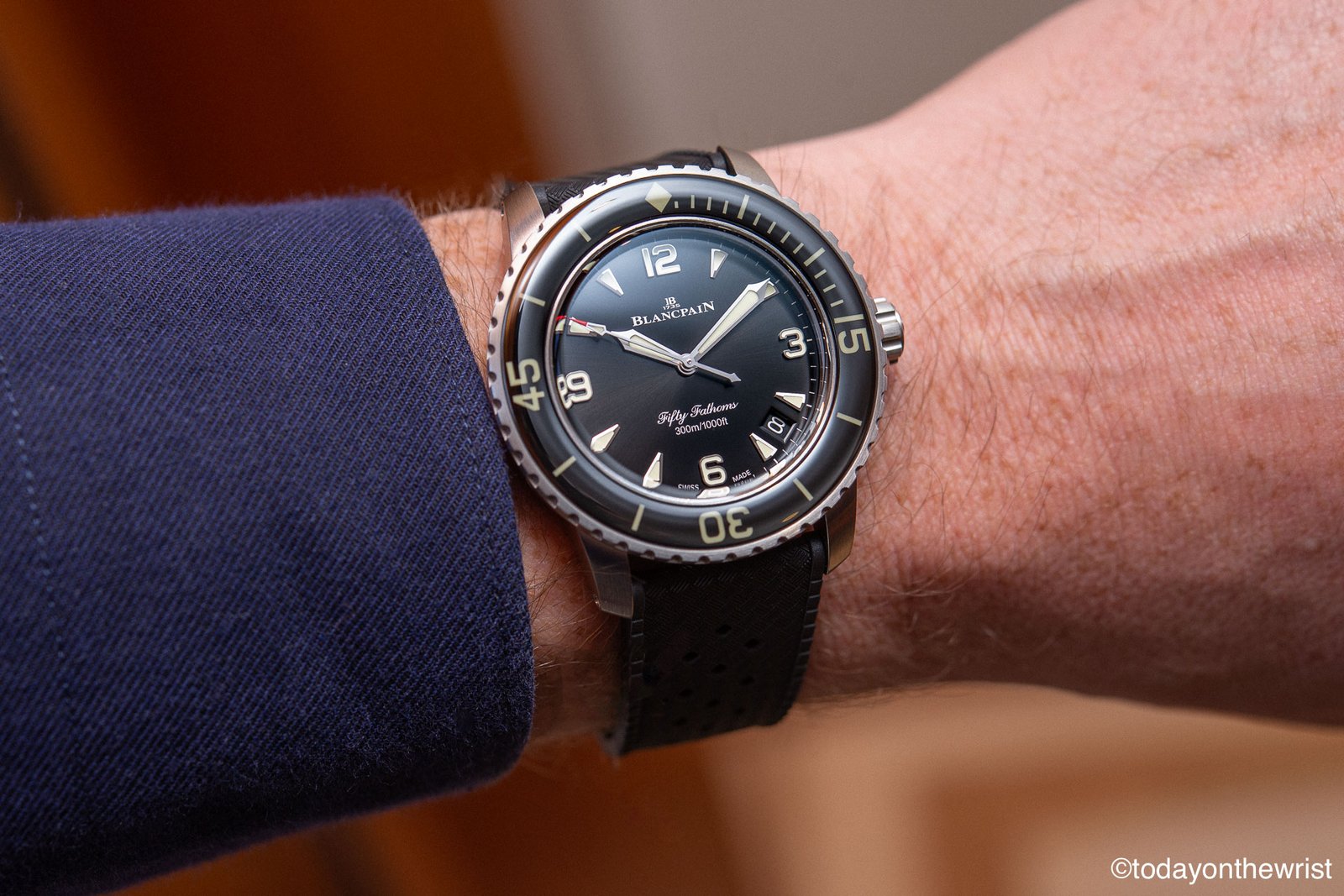
Big thanks to the Blancpain team for the invitation and the opportunity to experience Blancpain’s world from the inside. More details about Blancpain watches on www.blancpain.com